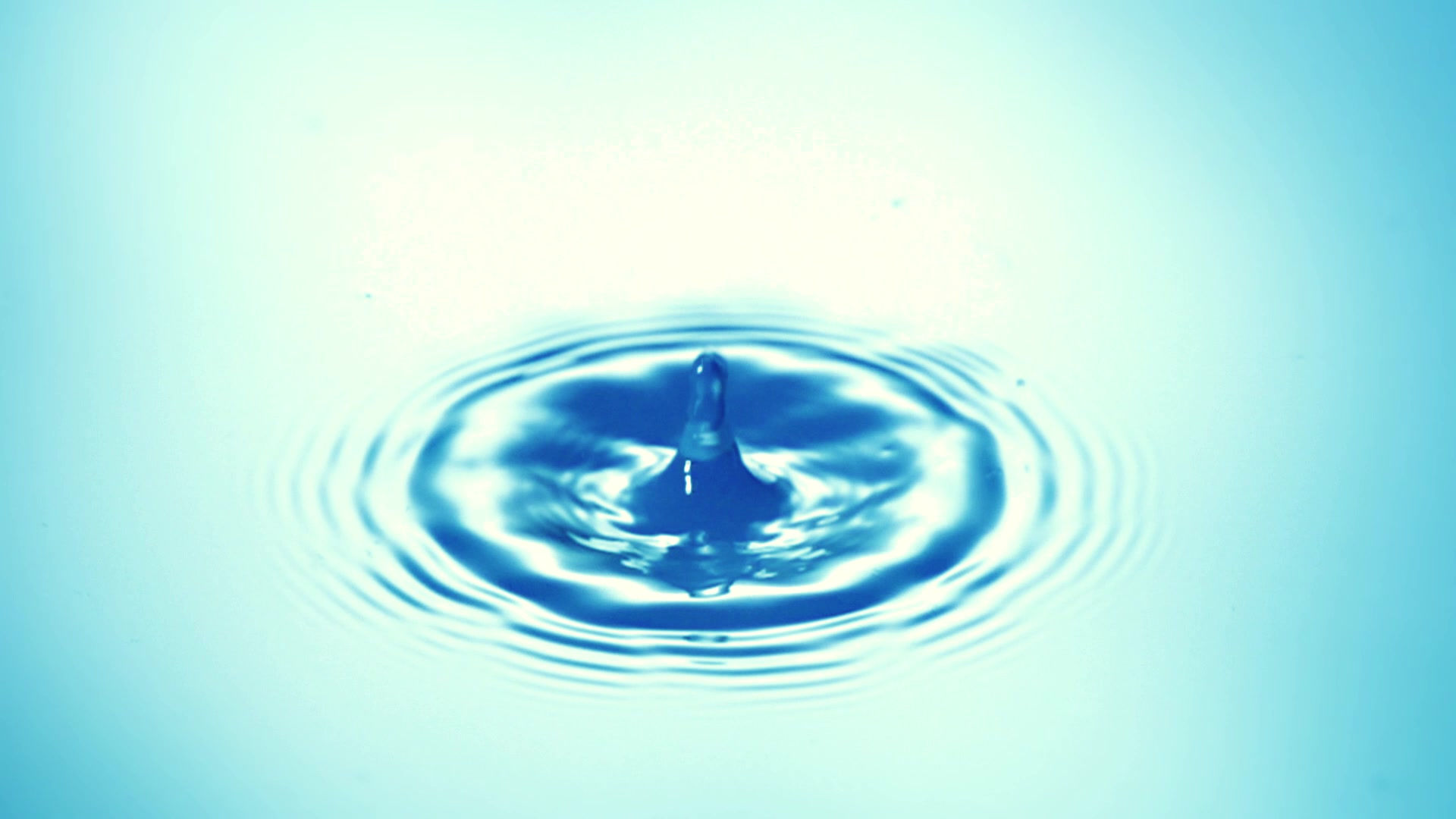
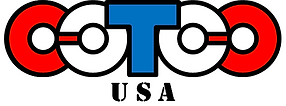
OCT COMPANY, INC.
"World-Class Production Chemicals Shipped from the East"
Oilsep® Paraffin Inhibitors
Paraffin Problems and Control
Production system has the potential of paraffin deposition when the temperature of the produced fluids falls below the wax appearance temperature. Paraffin treatments, such as crystal modifiers and pour point depressants, would help control paraffin deposition, thus maintaining pipeline and flowline integrity.
Field problems related to paraffin deposition include:
-
Paraffin Deposit Removal
-
Paraffin Deposit Inhibition
-
Crude Oil Pour Point Reduction
-
Pipeline Yield Value and Restart Pressure Reduction
-
Separator / Treater Interface Control
-
Tank Bottom Control
-
Inorganic Solids Wetting
-
Heavy Oil Transportation
-
Water Injection Well Clean-up and Maintenance
-
Organic Skin Damage Remediation / Production Stimulation
Viscosity
Crude oil increases in viscosity (thickness) as it is cooled. Considerable viscosity increase will take place as the oil is cooled to within 10 - 20F of the pour point. This will cause increased pumping pressure in the pipeline. PPDs can decrease the viscosity of a crude oil but only if it is in the high viscosity area within 10 - 20F of the pour point. If system temperatures are well above the pour point of the oil, PPDs will have little or no effect on the viscosity.
Yield Value Reduction
If the oil gets cold enough to solidify and the system is shut down for any reason, it may be difficult or impossible to restart the flow on production is resumed. Some systems even have insulated or heat-traced lines to protect against this. A crystal modifier can be used to reduce the pour point of the crude and/or reduce the gel strength of the solidified crude.
Each production system is unique. A customized paraffin control program should be designed to meet production challenges in a specific system using one or more of the following products:
-
Crystal modifiers or pour point depressants, which change the paraffin crystal structure and prevent them from forming a deposit
-
Dispersants, which keep the paraffin solids suspended in produced fluids
-
Solvents, which dissolve deposits that have formed prior to a chemical application
Paraffin Inhibitors
There are three main types of conventional paraffin inhibitors:
-
Ethylene vinyl acetate (EVA) polymers
-
Alpha-olefin maleic anhydride (OMAC) polymers
-
Ester type of paraffin inhibitors
-
polyacrylate
-
polymethacrylate
-
Paraffin Inhibitor Test Method
There are a number of techniques can be used to evaluate paraffin inhibitor's performance for a particular application.
-
Cold Finger Test
-
Well established lab/field dose rate correlation
-
-
Dynamic Tube Blocking Test
-
Evaluate paraffin inhibitor/dispersant performance
-
Absolute pressure and differential pressure measurement
-
-
Rheometer Test
-
Various geometries for different applications
-
Viscosity measurement
-
Pour point depressant performance evaluation
-
Yield stress, restart pressure calculation
-
Paraffin Inhibitor Application
Clean the System First: Paraffin inhibitors prevent paraffin deposition but do not remove existing deposits. The system should first be cleaned using removal methods.
Key to a successful paraffin inhibitor application is to inject the chemicals as upstream as possible in the production system. Continuous downhole injection is preferred because the chemical mixes with oil which is probably above its cloud point (wax appearance temperature) so the waxes are still in solution and the chemical can work on modifying the crystal structure of the wax when it first comes out of solution.
Continuous injection at the wellhead is the next best alternative. If there are no paraffin problems in the system until the oil goes into storage tanks and cools, then continuous injection at the outlet of the treater is acceptable.
The only potential problem with continuous injection is the physical properties of crystal modifiers. Some products can have high pour points, for expample above 100F. There are three ways to solve the physical property problem:
-
Heated storage
-
Large wells, large fields, and refineries all over the world use heated tanks to store PPDs.
-
In smaller fields, drum heaters can be used or the drums can be kept in a heated shed with heat-traced lines running to the wells.
-
-
Squeezing
-
Crystal modifiers can be squeezed into the formation and feed back continuously. This eliminates the need for pumps or heated storage.
-
Size of the squeeze treatment and overflush can be calculated using computer programs
-
-
Dilution
-
Crystal modifier can be diluted at the plant or by the operators on site to reduce its pour point.
-