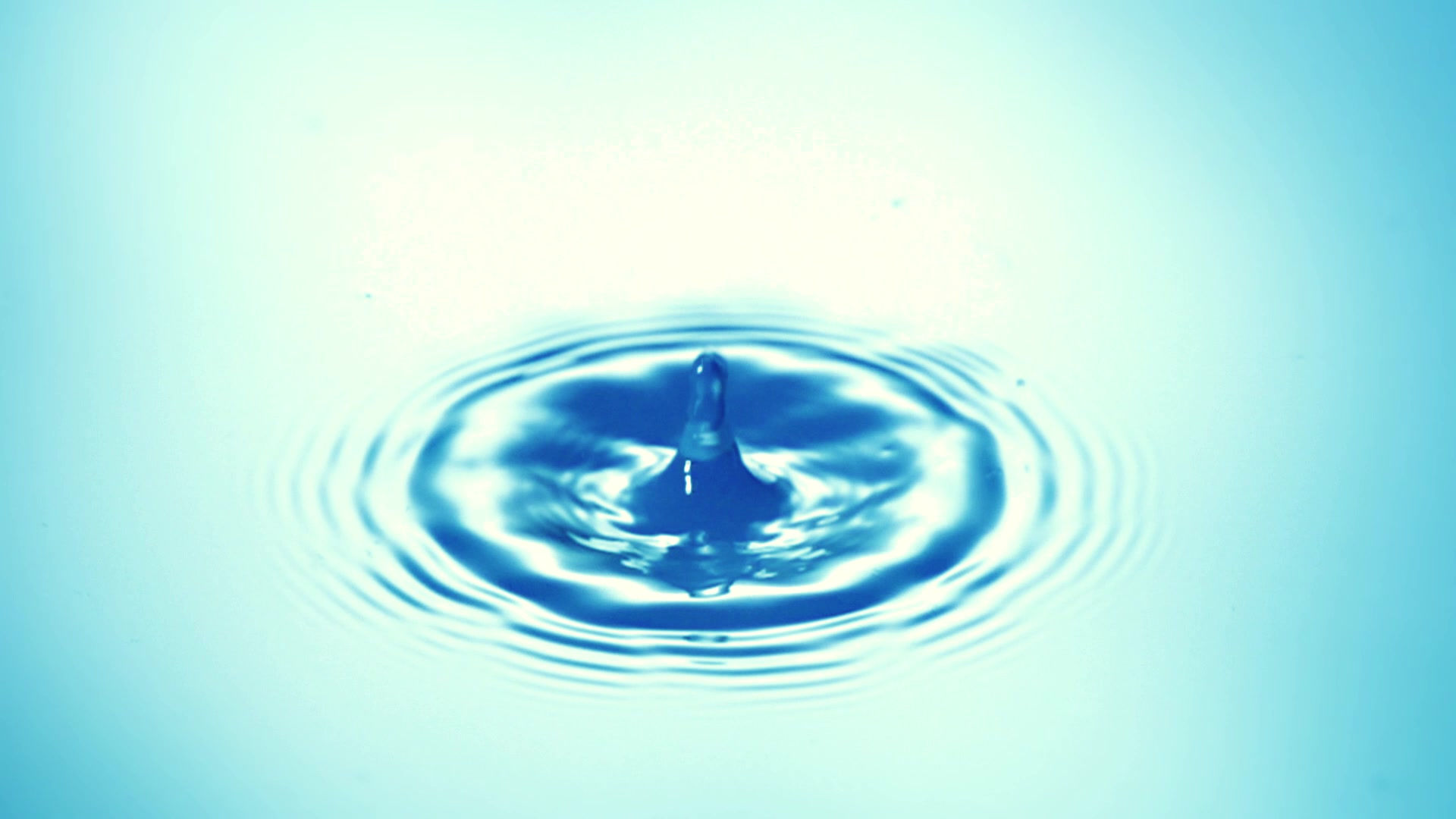
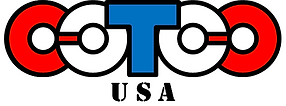
OCT COMPANY, INC.
"World-Class Production Chemicals Shipped from the East"
Fracturing Additives
Fracturing additives inlcude:
-
Surfactant to enhance oil/gas/water recovery
-
Biocide
-
Scale Inhibitor
-
Friction Reducer
-
Friction Reducer Breaker
-
Oxygen Scavenger
-
Clay Stabilizer / KCl Substitute
Surfactants
What are surfactants?
Surfactants are Surface Active Agents. They are molecules that are attracted to surfaces / interfaces (gas/liquid, liquid / liquid or liquid/solid). Surfactants would change or affect surface tension and/or interfacial tension, capillary pressure and wettability.
Over the years, a set of systematic methods has been developed to select the most cost effective surfactant for specific reservoir conditions. We believe the right surfactant should:
-
be tolerant to hard water at high TDS
-
be insensitive to temperature fluctuation in reservoirs
-
have correct surfactant chemistries for optimized interactions with oil
Carefully selected surfactants would reduce formation damage and restore formation permeability. Field fracturing applications have proved that:
-
Weakly emulsifying surfactants are more efficient in extracting the oil or condensate than conventional non-emulsifying surfactants
-
Field cases suggest that correct application of weakly emulsifying surfactants leads to better well cleanup and a higher oil and gas recovery
-
Pumping rates of the surfactants must be optimized to enhance production
Fracturing Surfactants Foundamentals
Capillary Pressure
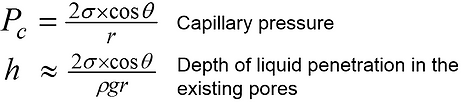
High Pc leads to water block (h) in the formation if reservoir pressure is not high enough to compensate for Pc, resulting in formation damage.
To maximumly restore reservoir's permeability after facturing by reducing the capillary pressure and increasing the flow area for oil and gas, the surfactant should be able to
-
increase the contact angle of the treating fluid
-
lower the surface tension of the treating fluid
Non-Emulsifying Vs. Weakly Emulsifying Surfactants
-
SPE paper 116237 compared averaged 12-month production in the DJ basin of 32 wells treated with a non-emulsifying surfactant and another 32 wells treated with a emulsifying surfactant. Those treated with emulsifying surfactant yielded 10% more condensate and 25% more gas.
-
SPE paper 154242 did another field test comparing a non-emulsifying surfactant with a weakly emulsifying surfactant on 6 wells in Eagle Ford. If the first 45 days, the three wells treated with the weakly emulsifying surfactant produced 25% more oil and 50% more gas than the other three wells treated with a non-emulsifying surfactant.
Biocides
Same types of production biocide chemistries would work in hydraulic fracturing. In addition to those considerations on production side, there are several more things to consider.
-
In slickwater fracturing or hybrid fracks including slickwater, the biocides need to be compatible with friction reducers. Incompatible biocides would break down high MW friction reducers resulting in high pumping pressures.
-
In sensitive areas, biocides need to be more environmentally friendly.
-
In deep reservoirs, more thermally stable biocides are required.
Scale Inhibitors
Scale inhibitors for hydraulic fracturing:
-
Must be compatible with other components in the frack fluids
-
In slickwater fracturing, most incompatibility issues occur with the polymeric friction reducers and manifest as pressure or solubility problems
-
Many scale inhibitors are not compatible with heavy metal crosslinkers in gel systems
-
The interference affect performance of both scale inhibitors and crosslinkers
-
-
-
Must withstand temperatures encountered during frac operations
-
Must be compatible with frac water with and without minerals dissolved during frac operations